Based on the reactions from guests at a twine-cutting ceremony, the designs of three cow sculptures on the lawn outside the new Ellsworth Cooperative Creamery cheese factory in Menomonie are spot-on.
The life-size Holstein creations, made of stainless steel pipes and stainless steel sheeting, indeed have classic Wisconsin dairy cow features — big spots, floppy ears and even cowbells hanging from their necks as they take familiar positions, one grazing, one resting and one, a calf, standing.
The ceremony in September celebrated the culmination of a yearlong collaborative project with the creamery and UW-Stout. It also capped off spring projects in which more than 60 students from the School of Art and Design — along with packaging and engineering majors — experienced firsthand their future careers by working with actual clients.
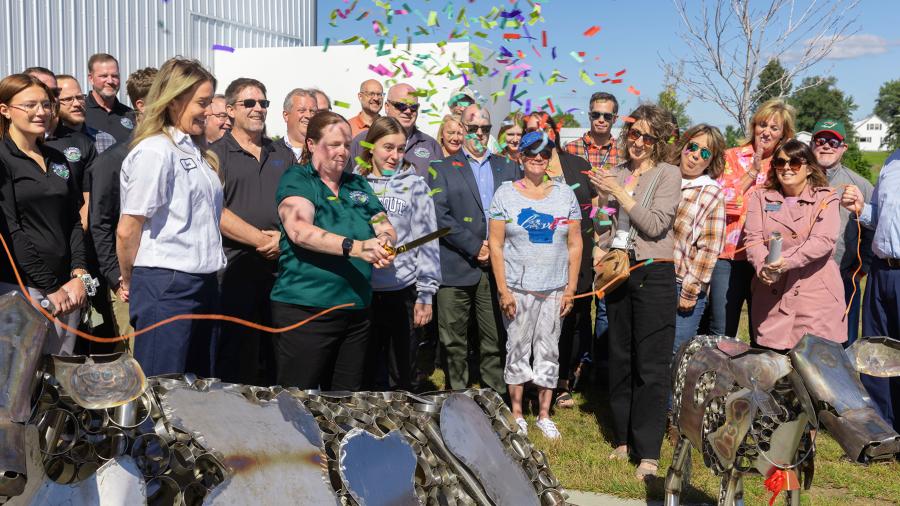
“This project really shows what we’re about at Stout as a polytechnic university,” said Chancellor Katherine Frank, who spoke at the ceremony. “Our students apply their learning and work through challenges with business and industry partners to bring their creative ideas to life.”
The cows are made of recycled material, part of the creamery’s sustainability goals to eliminate waste: the pipes left over from building the facility are the “bones”; thin sections cut from the pipes, or rings, welded together make up much of the “hides”; fabricated pieces of the sheeting, from a processing trough where cheese is stirred and separated from whey, are the “spots,” “ears” and “heads.”
The hundreds of rings took three to six minutes each to cut and debur.
“The project took a lot more time than I thought it would, but it also was a lot more fun. It was a great project to bring into the classroom,” said Renae van der Hagen, of St. Cloud, Minn., a senior in industrial and product design.
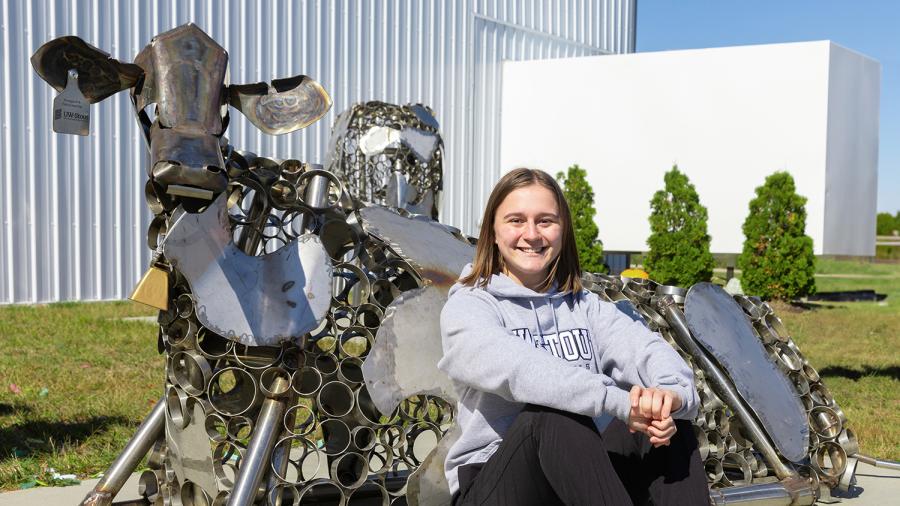
Project timing was perfect for van der Hagen: She was taking a welding class with Assistant Professor Nathan Spike, engineering and technology, when the opportunity came up, and she had a sculpture class the semester before. However, she didn’t have experience with stainless steel. “There were a lot of learning curves there for the design process,” she said.
She was one of five seniors on the fabrication team, along with Dominick Konkel, of Hokah, Minn., mechanical engineering; and three other industrial and product design majors, Sam Bachofen, of Waterford; Bryan Irish, of Hazelhurst; and Daniel Neve, of Mound, Minn.
Along with the students, Deano Samens, instrument shop coordinator in the Process Lab of School of Art and Design, and Spike helped fabricate the cows in a lab. The team made wispy tails of steel cable, and the cows’ heads rotate.
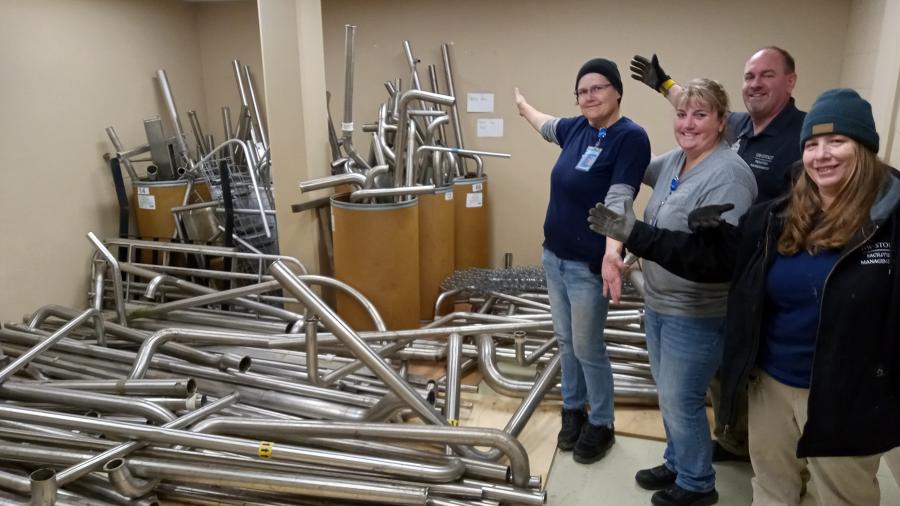
“It takes a little vision to look at a pile of pipe and think, ‘Hey, what if we make some cows out of this?’ Samens told the several dozen people who gathered on the lawn next to the cows — a place for future customer photo opportunities. “There was a whole lot of cutting, torching and bending, welding and grinding mixed with sheer tenacity to bring this family of cows to fruition.”
The group visited Joel and Mindy Eckert’s Bountival Farm near Menomonie to get cow measurements and a better feel for what they were about to create.
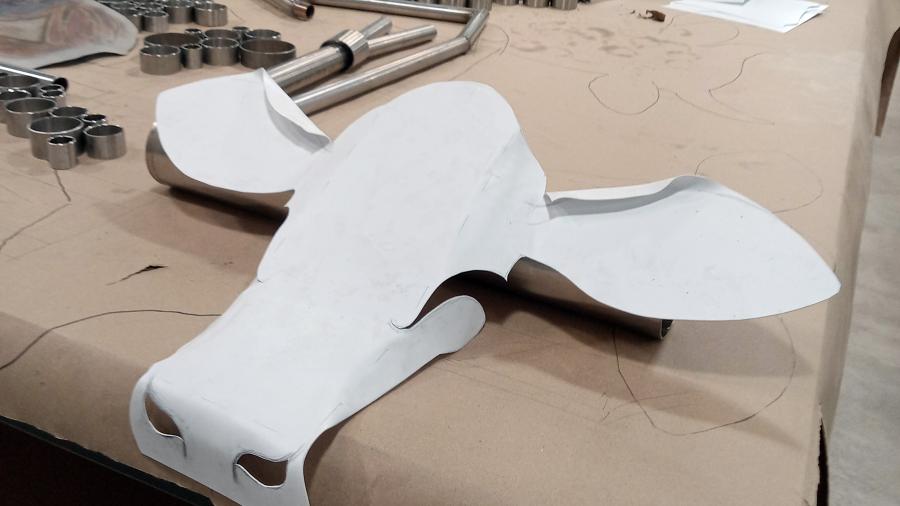
Original concepts for the cows were created in a fall 2023 class, Design Theory and Methods, taught by Dan Banasik. More than 20 students first made scale models of their ideas, then full-scale models out of cardboard. The ideas were reviewed and narrowed down by Ellsworth Cooperative Creamery before production began.
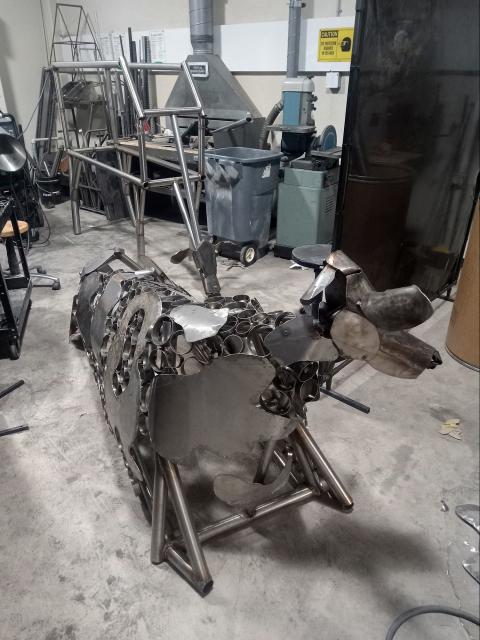
“These sculptures are a wonderful reflection of how we come together to approach challenges at the Ellsworth Creamery Cooperative with innovation and collaboration,” said John Freeman, assistant director of marketing for the company. “It’s incredible to see the UW-Stout students use their imagination and skills to turn what might be considered scrap metal into a work of art.”
Ellsworth’s Menomonie plant produces block cheese while the Ellsworth plant makes the company’s famous curds, although all cheese begins as curds, Freeman said. The new facility, which is on Highway B just north of Interstate 94, includes a retail shop with food service, a cheese production viewing area and a patio area with the cow sculptures.
The project was coordinated through UW-Stout’s Office of Corporate Relations and Economic Engagement, led by Executive Director Seth Hudson; and Professor Tamara Brantmeier in the Provost’s Office and School of Art and Design.
Hudson, Brantmeier, Frank and Provost Glendalí Rodríguez initiated talks with the creamery about using university expertise to engage on projects, resulting in the creamery suggesting the sculpture project. Brantmeier identified key faculty and staff members, including Samens and Spike, to lead the work.
“We worked closely with the OCREE team, which offers amazing support for external partner projects like these,” Brantmeier said.
Through OCREE, UW-Stout continues to seek projects from industry and community partners that can be brought into the classroom. Learn more here.
Product displays for Great Northern and Athena Club
Last spring, students from the graphic design and interactive media program paired with packaging majors to take on a dual challenge: Help Great Northern Corp. develop product displays for one of its clients, Athena Club of New York.
Athena Club makes women’s razor kits and other self-care essentials. It began as an online company and is expanding to retail sales. Great Northern designs and manufactures retail product displays.
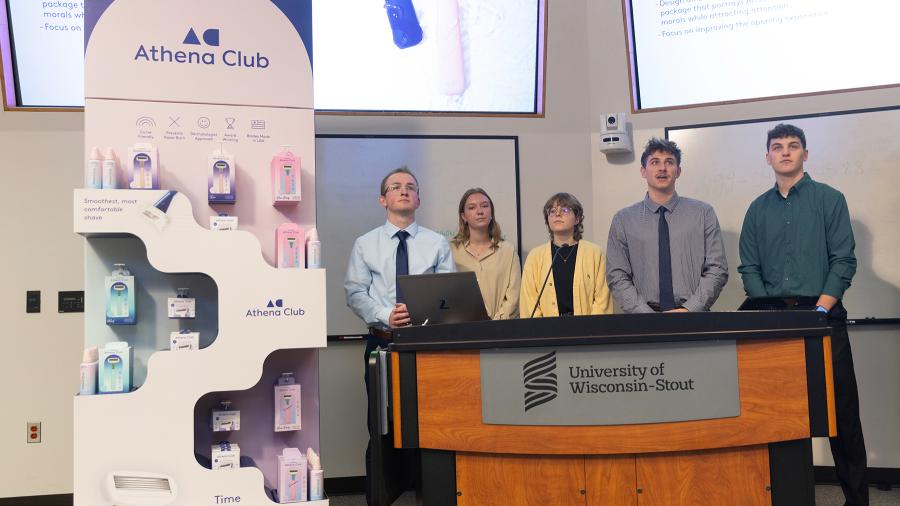
Fifteen packaging and 10 graphic design student, five teams, worked throughout the spring semester, from ideation to presenting their final concepts during presentations on campus. Great Northern and Athena Club officials, who worked virtually and in person with students as the projects progressed, attended the presentations and provided feedback.
Students designed new product packaging for the razor kits and refill kits along with the vertical display cases, ranging from 5 to 7 feet tall, that held the products. Packaging students created the packaging and display structures; graphic design students made them appealing.
They had to consider market research, brand, user experience, structural design — will the display case be easy to ship and set up for retailers and hold enough product without collapsing? — and other factors.
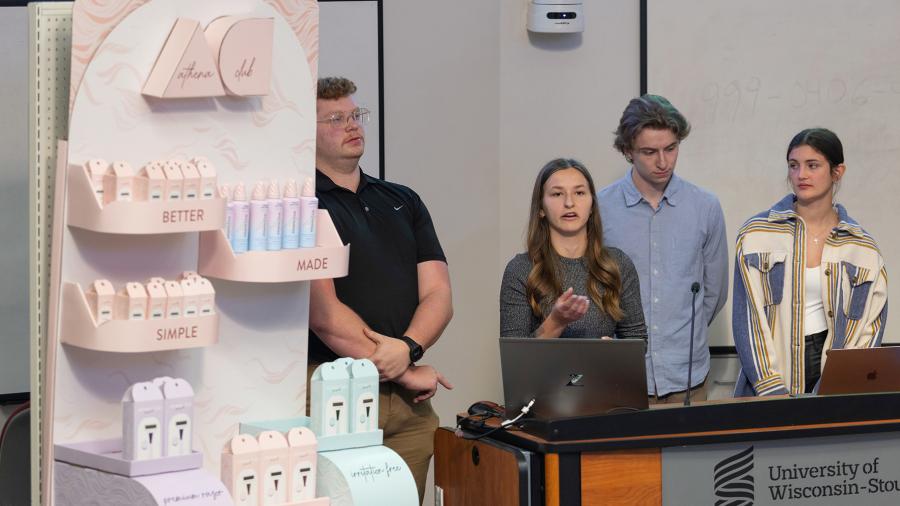
Ashley Jandro is a Master of Fine Arts in design major and earned a bachelor’s in 2022 from UW-Stout in graphic design with a focus on 2D advertising concepts. “This project made me think in a 3D world, about user experience, how people interact with a product and why,” Jandro said.
Plus, working with packaging engineers and with a real client presented additional learning curves that she said have made her a better designer.
Great Northern employs about 30 UW-Stout alumni. The Appleton-based company manufactures packaging and retail displays and has operations in five states, with Wisconsin locations in Appleton, Chippewa Falls and Racine. It has more than 1,700 employees.
In 2020, the company committed $100,000 in funding toward the sponsored course, to be held multiple times over four years. This year, it committed another $100,000. The gifts for the course have been coordinated through Stout University Foundation.
Packaging program director and Associate Professor Min DeGruson and Professor Nagesh Shinde from the graphic design program led the course, a senior capstone for packaging and an advanced design selective for graphic design students. “It’s really a challenging project for students, but at the end of the day they learn a lot,” DeGruson said.
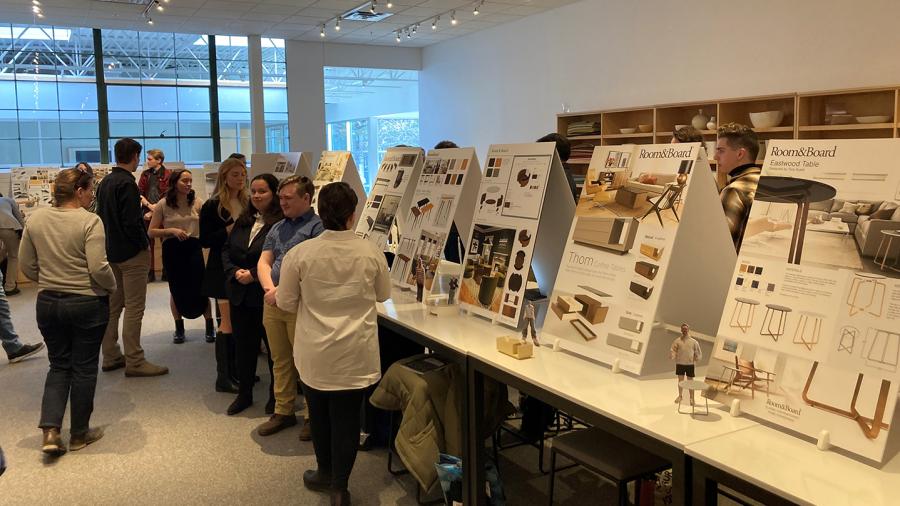
Furniture concepts for Room & Board
In an industrial and product design senior capstone course taught by Lecturer Emily Pieper, 28 students developed 28 accent piece concepts for Room & Board during a three-week project.
Designers from the Minneapolis company came to UW-Stout to kick off the project and visited again two weeks later. Then, students went to Room & Board to present their final ideas, including gallery-style posters detailing their design process and 1/16th scale models of their designs. The models were 3D-printed.
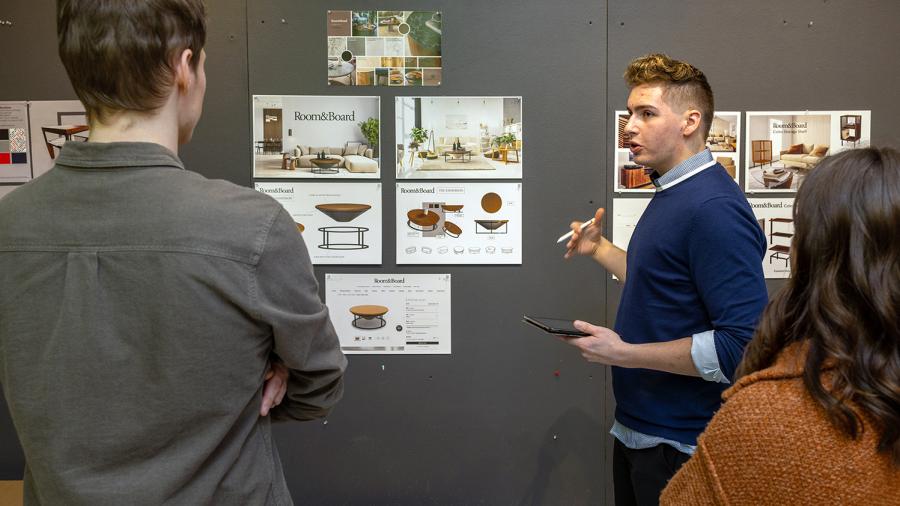
Several of the students’ ideas could become the basis for new Room & Board products.
“This project taught me a lot,” said Kate Dieckman, who revealed a coffee table design idea during student presentations at the headquarters of furniture-maker Room & Board in Minneapolis. “I learned that the client's opinion is what truly matters and hitting their goals trumps my own.”
Dieckman, a senior from Menomonie, designed a midcentury modern coffee table. “The objective to create an accent piece of furniture that could seamlessly integrate with the existing Room and Board collection and brand aesthetic,” she said.
“Room and Board’s design restrictions were based around aesthetics and trying not to reinvent the wheel. Research of the company had to be done to understand what they were aiming for. Their brand is known to be high quality, long-lasting and simple timeless styles. Due to this, our designs reflected that and were simple in form but elevated in details like joinery,” Dieckman said.
###