Students in a New Product Development course at UW-Stout recently completed a 3 1/2 week project developing toolless bed connections for Ashley Furniture Industries, LLC (Ashley), a global leader in furniture manufacturing.
The project kicked off on April 15, when Ashley Research and Development (R&D) team members presented the project virtually to the 18 students in Assistant Professor Kevin Dietsche’s class.
Over the next few weeks, the students worked in eight cross-disciplinary groups to research market trends, ideate preliminary designs, test materials and build professional prototypes. They received mentorship along the way from Ashley product designers.
The class then traveled to Ashley in Arcadia on May 6, for a tour of the facility and to present their prototypes to the R&D team.
“This was an incredible experience – one that stood out for its real-world relevance and industry collaboration,” mechanical engineering major Alex Springer said. “Working directly with professionals from Ashley – one of the biggest companies in the furniture industry – gave us insight into the complete product development cycle, from initial design through manufacturing and packaging to mechanical and interior design to align functional and aesthetic goals.”
Ashley Furniture Industries is the world's largest furniture manufacturer with more than 35,000 employees worldwide, providing product to 20,000 storefronts in 155 countries, and operating over 1,100 Ashley retail stores in 70 countries.
Dietsche was awarded a sponsorship by Ashley to fund the project.
Preliminary research and feedback
Ultimately, each group wanted to create a unique product that was budget-friendly, sturdy and easy to assemble right out of the box – a main goal of the toolless bed connection concept.
They began by conducting market research to view current Ashley products and prices, as well as those of competitors and DIY models online. They factored in pricing of materials, such as medium density fiberboard (MDF) and particleboard, to save on costs, looked at estimated labor, manufacturing, storage, shipping and more compared to selling cost.
Several groups conducted surveys to find where consumers prefer to buy their furniture, how much they are willing to spend on a bed frame and how much time they expect to spend on assembly.
When looking at styles of joinery in woodworking, groups based their initial digital designs on mortise and tenon joinery with locking pins, castle joints and Japanese wedge joints.
Some groups simulated tests on the strength of MDF board and particleboard, testing different thicknesses for weight allowances. Other groups “over-built” their designs according to the FEA – finite element analysis – factor of safety, to measure how well a design could withstand a load.
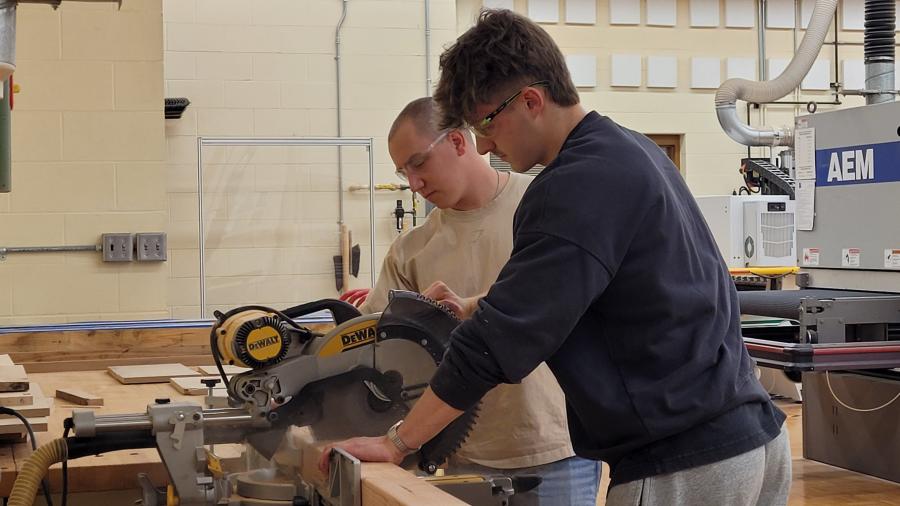
One group – Springer and fellow mechanical engineering major Jered Clark, and packaging majors Luke Janssen and Sam Petkovsek – drafted a Computer Numerical Control, or CNC, model for automated machining of sideboards, slots, pins and legs, based on mortise and tenon joinery. They estimated a run time of 12 minutes to complete a bedframe.
Another group – mechanical engineering major Owen Coon and engineering technology major Kadence Tinsley – designed 3D-printed interlocking brackets using SolidWorks software. They also wrote an AI prompt to generate images of bed frames for college-age consumers. They estimated their design would have a 50% profit margin.
Technology education major Annika Schlueter and engineering technology major Hunter Ouimette built a scaled model of an interlocking Japanese wood joint bedframe using CNC for manufacturing the larger parts because it is more efficient and cost-effective. They also implemented two different types of locks – a wedge and a 3D-printed ring – for different aesthetic looks.
Ashley product designers Angel Kraemer, Caleb Toft and Anna Lindner, all UW-Stout industrial and product design alums, provided feedback, including encouraging the groups to think about usability and flexibility for multiple looks depending on a consumer’s individual style.
They asked the groups to understand the materials used and how different environments can impact MDF board versus particleboard, such as temperature and climate tolerance, as well as to consider how the different materials, such as MDF versus wood, handle tooling and manufacturing. A joint design in one material may be more difficult to produce in another.
Designing under a deadline
Dietsche uses the Design Build Process – a model for teaching projects with quick turnaround times. “When you give students such a fast deadline for large-scale projects, when you cram them with ideas, it forces creativity. There’s this crash and burn and rebuild mentality. They’ll make mistakes and learn to quickly find solutions. It can be stressful, but it builds grit.”
Schlueter thinks one of the biggest benefits of this teaching/learning approach is the need to be creative and take advantage of the time given, with only four to five class periods to research, test, fully develop a model and be ready to present. “No team’s design has stayed the exact same since we started the toolless bed connection project. Things go wrong, and things go right, and we had to develop accordingly,” she said.
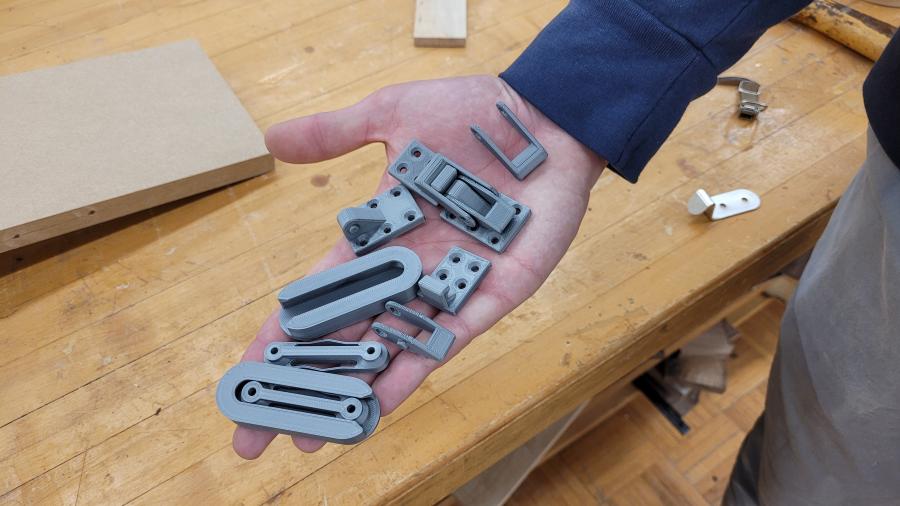
Springer, Petkovsek, Janssen and Clark’s group had to pivot away from their original design of mortise and tenon joinery when Ashley’s designers recommended that they use fasteners to secure the frame to the legs instead of wood joints. This tested the group’s adaptability, Springer said.
“Ashley sent us some ideas for fasteners, and they served as a model for ours. After researching, we bought one model of metal fasteners and designed two custom models of fasteners – a slot and lock; and a hook and clamp,” added Clark, who printed the group’s models on his 3D printer at home.
The group designed multiple iterations of their fasteners. The first prototype failed to hold securely under tension. The second performed better but still slipped under stress. “Our final design addressed those weaknesses, significantly improving grip and structural stability. I think if we were able to continue the project, we would look into stronger plastics and possibly metal to enhance the durability of our clips,” Springer said.
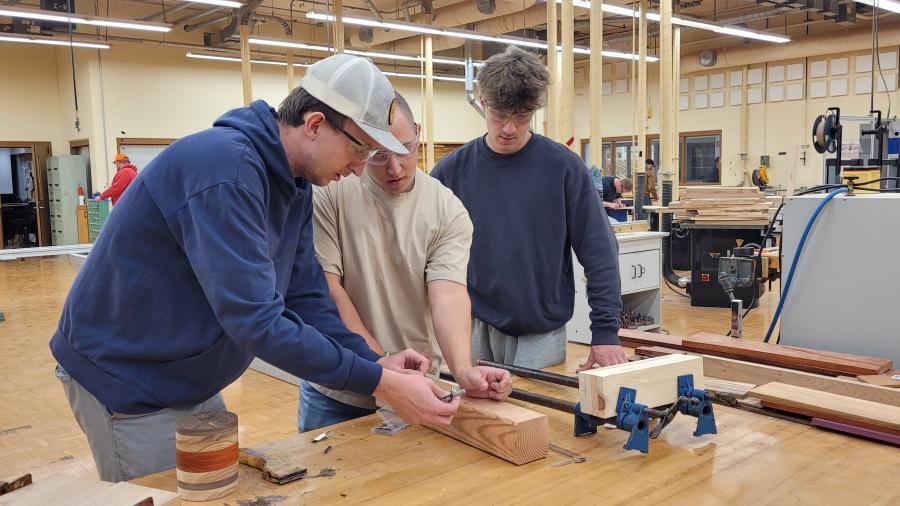
In the Jarvis Hall Technology Wing Woods Lab, the group built and tested a full-scale queen-sized prototype using MDF and chipboard for the frame and 4X4s for the posts. Working with MDF introduced material-specific hurdles, such as expansion and contraction, which affected their product’s fit tolerances.
They also developed a corrugated branded packaging solution using UW-Stout’s Packaging Lab in the Applied Arts Building and designed an assembly booklet for customers. “It was an all-around lightbulb moment to see the mechanical engineering and packaging phases of our project come together,” Springer said.
Making an impact on manufacturing
Dietsche and the Product Development class traveled together by bus to Ashley on May 6. They were given a tour of the facilities, including a visit to the Advanced Technology Maker Center, the Automation and Robotics Laboratory, and the design and R&D departments.
The eight groups then gave PowerPoint presentations of their designs and discussed their physical prototypes with the R&D team.
Springer, Petkovsek, Janssen and Clark are proud of their final outcome. Along with their functional full-size bed frame, they also delivered a professional mini model to showcase during their presentation.
“Given the timeline and complexity, we’re delighted with what we accomplished. We were excited to get feedback on our project, especially the positive feedback from Ashley,” said Springer, noting that presenting to Ashley was a highlight of the semester.
“The project was an opportunity to make connections with different majors in the class, advance our CNC and manufacturing process skills and professionalism, and have fun while doing something that could be very impactful for a large company,” Schlueter added.
UW-Stout’s engineering and technology department offers six undergraduate degrees, including computer and electrical engineering, manufacturing engineering, mechanical engineering, plastics engineering, engineering technology and packaging, as well as four minors and a master’s in manufacturing engineering.
Technology education is offered through the School of Education, which is home to nine undergraduate degrees, five graduate degrees, certificates, certifications and online professional development courses.